|
|
|
|
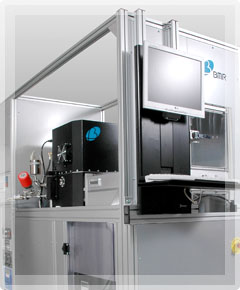 |
 |
DFS-200, BMR Technology Corporation’s plasma
asher, is a downstream plasma asher designed for
plasma-damage-free photoresist ashing based on
proprietary inductively coupled plasma technology.
Its unique capability of tight wafer temperature control
makes DFS-200 particularly useful for photoresist
ashing of temperature sensitive devices.
DFS-200’s fully automated vacuum cassette wafer
loading system provides cost-effective high throughput
photoresist ashing for mass production. |
|
|
 |
Proprietary Inductively Coupled Plasma (ICP)
Technology |
Low DC & RF plasma potentials |
Downstream plasma with an optional ion grid |
Plasma-damage-free photoresist ashing with high ashing rate |
Electrostatic Chuck for accurate control of wafer temperature |
Low temperature process (<100 ) capability for temperature sensitive microelectronics devices. |
Vacuum cassette wafer loading system |
Accurate process pressure control |
Easy-to-use control software with a recipe editor |
Ideal for cost-effective mass production |
|
 |
Process chamber made of 6061-T6 Aluminum billet |
Up to 200mm wafer |
Patented inductively coupled plasma source (ICP) for
efficient generation of oxygen radicals. |
Proprietary electrostatic filed shield for true inductive
coupling of RF power to plasma to prevent plasma damage due to electrostatic fields |
Optional ion shield to prevent ion-induced plasma damage
Dry vacuum pump |
Controllable process pressure ( 200mTorr ~ 5 Torr )
1.2 KW RF Power Supply @ 13.56MHz with an automatic match network |
Bipolar type electrostatic wafer
clamping |
Wafer temperature controllable from room temperature to 200 |
Two Mass Flow controlled gas lines |
Photoresist ashing rate > 7500 /min. |
|
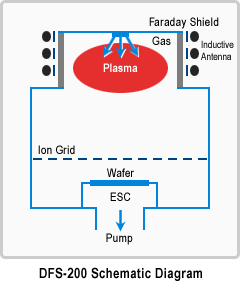 |
|
Windows 2000 based graphic user interface (GUI) |
Automatically controlled 25 wafer cassette loading in vacuum. |
A dedicated dual-stage rotary vane pump for cassette loading chamber |
SECS I, II/GEM Interface |
|